Vận hành dây chuyền vữa khô dưới góc nhìn chuyên gia không chỉ đòi hỏi hiểu rõ vệ hệ thống thiết bị, mà còn biết cách kiểm soát chặt chẽ các thông số kỹ thuật để đảm bảo vận hành hiệu quả. Bài viết chia sẻ dưới đây nhất định sẽ giúp các chủ đầu tư, doanh nghiệp hiểu rõ hơn về quá trình vận hành dây chuyền sản xuất.
1. Tầm quan trọng của vận hành dây chuyền sản xuất vữa khô
Trong ngành xây dựng hiện đại, dây chuyền sản xuất vữa khô đóng vai trò quan trọng trong việc cung cấp vật liệu trộn sẵn, đáp ứng nhu cầu từ các dự án quy mô lớn như cầu đường và khu đô thị. Với chất lượng ổn định và khả năng tối ưu hóa hiệu suất, việc vận hành dây chuyền sản xuất vữa khô đòi hỏi sự hiểu biết sâu sắc về cấu tạo, chức năng và quy trình kỹ thuật của hệ thống. Một ca làm việc tiêu chuẩn thường bắt đầu lúc 8h sáng và kéo dài 8 tiếng, nhưng trong các dự án cấp bách, dây chuyền có thể hoạt động liên tục 16-24 tiếng/ngày.
Cùng tìm hiểu về các bộ phận chính của dây chuyền sản xuất vữa khô, bao gồm chức năng, phương thức hoạt động, thông số kỹ thuật, sự cố tiềm ẩn và lưu ý khi vận hành.
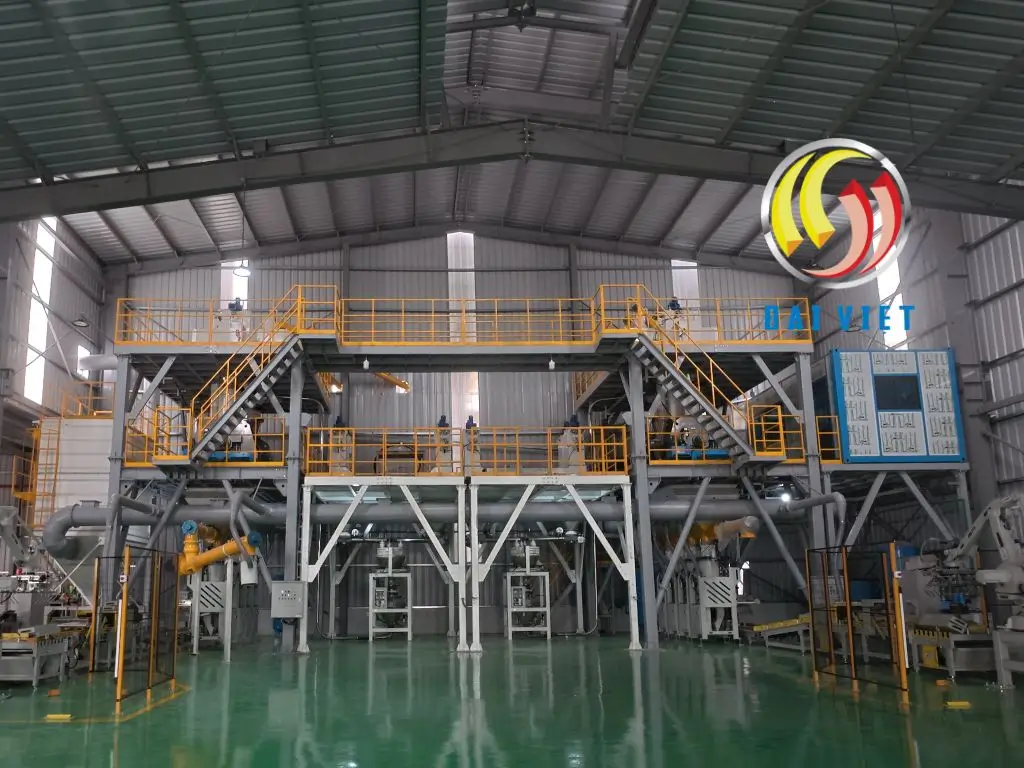
Hình ảnh dự án dây chuyền sản xuất vữa khô và keo dán gạch ở Phú Thọ – Bước đầu chuẩn bị vận hành dây chuyền vữa khô
2. Cấu tạo chi tiết của dây chuyền sản xuất vữa khô
Dây chuyền sản xuất vữa khô là hệ thống khép kín gồm nhiều bộ phận liên kết chặt chẽ. Dưới đây là phân tích chi tiết về cấu tạo và vai trò của từng thành phần. Một dây chuyền sản xuất vữa khô với quy mô công nghiệp áp dụng công nghệ hiện đại thường bao gồm các module:
2.1. Hệ thống chuẩn bị nguyên liệu
- Cấu tạo: Silo chứa (dung tích 50-100 tấn, vật liệu thép carbon), vít tải trục ngang hoặc nghiêng (đường kính 219-323mm, dài 6-12m), phễu trung gian (dung tích 2-5 tấn).
- Chức năng: Lưu trữ và vận chuyển nguyên liệu thô như cát (kích thước hạt <5mm), xi măng (mác PC40 theo TCVN 2682:2009), tro bay và phụ gia đến các khâu tiếp theo.
- Phương thức hoạt động: Nguyên liệu được nạp vào silo thông qua hệ thống khí nén (áp suất 6 bar, lưu lượng 10-15 m³/phút). Vít tải quay với tốc độ 80-120 vòng/phút, vận chuyển nguyên liệu đến phễu trung gian với công suất 10-20 tấn/giờ.
- Sự cố tiềm ẩn:
- Vít tải tắc nghẽn do cát có độ ẩm vượt quá 0,5% hoặc lẫn tạp chất lớn hơn 5mm.
- Silo mất áp suất do van khí nén bị rò rỉ.
- Lưu ý: Khi vận hành dây chuyền vữa khô, cần sử dụng lưới sàng 5mm để loại bỏ tạp chất từ cát; kiểm tra áp suất silo bằng đồng hồ đo (phạm vi 0-10 bar) trước mỗi ca.
2.2. Hệ thống sấy cát
- Cấu tạo: Lò sấy thùng quay (đường kính 1,5-2m, dài 10-15m, công suất 10-50 tấn/giờ), động cơ điện 15-37kW (380V, 50Hz), quạt hút (lưu lượng 8000-15.000 m³/h), đầu đốt sử dụng nguyên liệu khá đa dạng như dăm gỗ, than, gas, điện hoặc dầu (nhiệt lượng 500.000-1.500.000 kcal/h).
- Chức năng: Làm khô cát từ độ ẩm ban đầu 2- 10% xuống dưới 0,5%, đảm bảo hỗn hợp vữa khô đạt độ đồng đều và không bị vón cục theo tiêu chuẩn TCVN 4313:2003.
- Phương thức hoạt động: Cát được đưa vào thùng quay thông qua vít tải với tốc độ 10-20 tấn/giờ. Đầu đốt tạo khí nóng, quạt hút đẩy hơi ẩm qua ống khói (đường kính 400mm) kết hợp hệ thống lọc bụi.
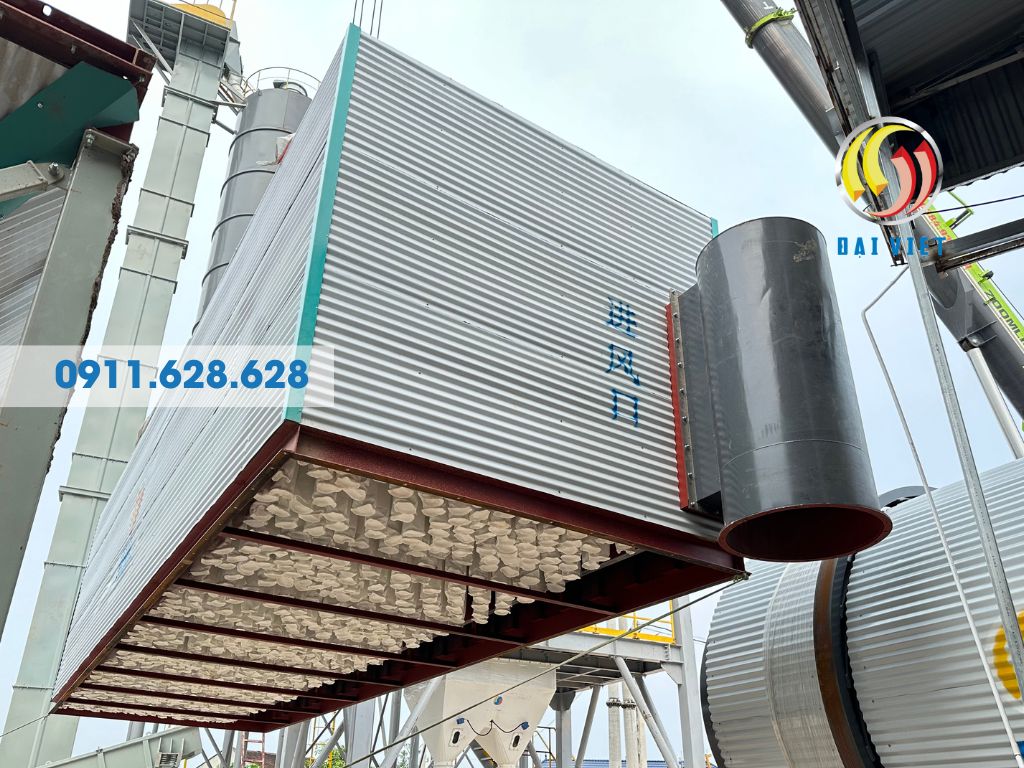
Hình ảnh túi lọc bụi của hệ thống thu bui vữa khô và keo dán gạch trong quá trình lắp đặt trước khi vận hành dây chuyền vữa khô
- Thông số kỹ thuật chính xác về nhiệt độ:
- Nhiệt độ khí nóng đầu vào:Từ khoảng 400 trở lên
- Nhiệt độ cát đầu ra: 60-70°C (đo bằng nhiệt kế hồng ngoại, sai số ±1°C, tối ưu để tránh ảnh hưởng phụ gia).
- Nhiệt độ tối đa cho phép: 85°C (vượt quá mức này có thể làm biến tính phụ gia polyme hoặc gây cháy bụi cát).
- Độ ẩm cát đầu ra: <0,5% (đo bằng máy đo độ ẩm chuyên dụng, sai số ±0,1%).
- Sự cố tiềm ẩn:
- Quạt hút giảm hiệu suất (cánh mòn sau 5000 giờ), làm nhiệt độ trong thùng tăng quá 70°C.
- Cảm biến nhiệt hỏng (sai số >0,5°C), dẫn đến đầu đốt hoạt động quá mức.
- Ống khói bị tắc bởi bụi dày hơn 5mm, giảm hiệu suất sấy 20-25%.
- Lưu ý:
- Điều chỉnh nhiệt độ khí đầu vào trong khoảng 400-500°C, đảm bảo cát đầu ra duy trì 60-70°C (kiểm tra mỗi giờ).
- Vệ sinh ống khói mỗi 7 ngày; bôi trơn vòng bi thùng quay bằng mỡ chịu nhiệt (NLGI 2) sau mỗi 500 giờ vận hành.
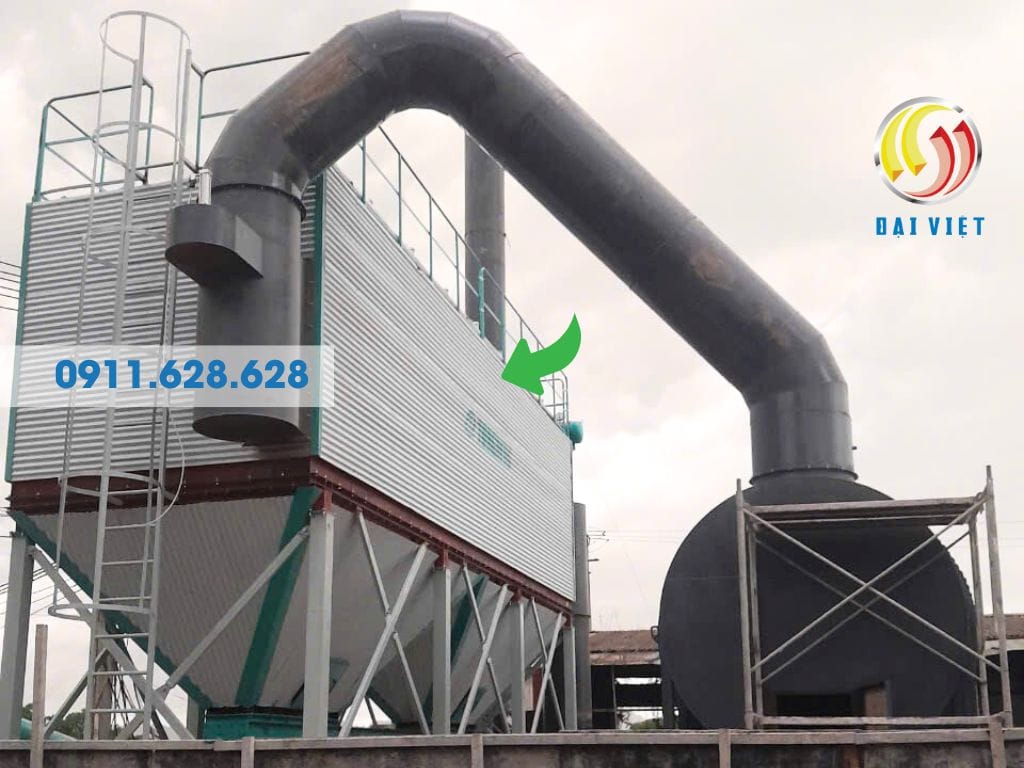
Hình ảnh hệ thống thu bụi bằng túi lọc dạng xung của trạm trộn vữa khô và keo ở Hà Nam trước khi vận hành dây chuyền vữa khô
2.3. Hệ thống cân định lượng
- Cấu tạo: Cân điện tử (tải trọng tối đa 5 tấn, sai số ±0,1%), cảm biến tải trọng (load cell, độ nhạy 2mV/V), phễu chứa (dung tích 2-5 tấn), van xả khí nén (đường kính 100mm).
- Chức năng: Đo lường chính xác khối lượng nguyên liệu theo tỷ lệ định sẵn (thường 70% cát, 25% xi măng, 5% phụ gia) để đảm bảo chất lượng phối trộn.
- Phương thức hoạt động: Nguyên liệu từ silo và lò sấy rơi vào phễu, cảm biến đo trọng lượng thông qua bộ điều khiển PLC. Van xả mở trong 0,5-1 giây mỗi đợt để chuyển nguyên liệu xuống máy trộn, với tốc độ cân 1-2 tấn/phút.
- Thông số kỹ thuật:
- Sai số đo lường: ±0,1% (tương đương 100g/1 tấn).
- Tần suất hoạt động: 60-120 mẻ/giờ.
- Sự cố tiềm ẩn:
- Cảm biến lệch (±0,5kg) do bụi bám dày hơn 2mm.
- Van xả kẹt do xi măng khô cứng khi độ ẩm vượt 1%.
- Lưu ý: Khi vận hành dây chuyền vữa khô, cần chú ý đến hiệu chuẩn cảm biến mỗi 90 ngày bằng quả cân chuẩn 1 tấn; vệ sinh phễu bằng khí nén áp suất 6 bar sau mỗi ca.
2.4. Hệ thống trộn
- Cấu tạo: Máy trộn một trục hoặc hai trục (dung tích 1-5 tấn/mẻ), động cơ 22-55kW (380V, 50Hz), trục quay (thép carbon C45), lưỡi trộn (thép chịu mòn, dày 8-12mm, góc nghiêng 45°).
- Chức năng: Trộn đều các thành phần nguyên liệu trong khoảng 5phút, đạt độ đồng nhất 1:10.000, đảm bảo tính chất cơ lý của vữa khô.
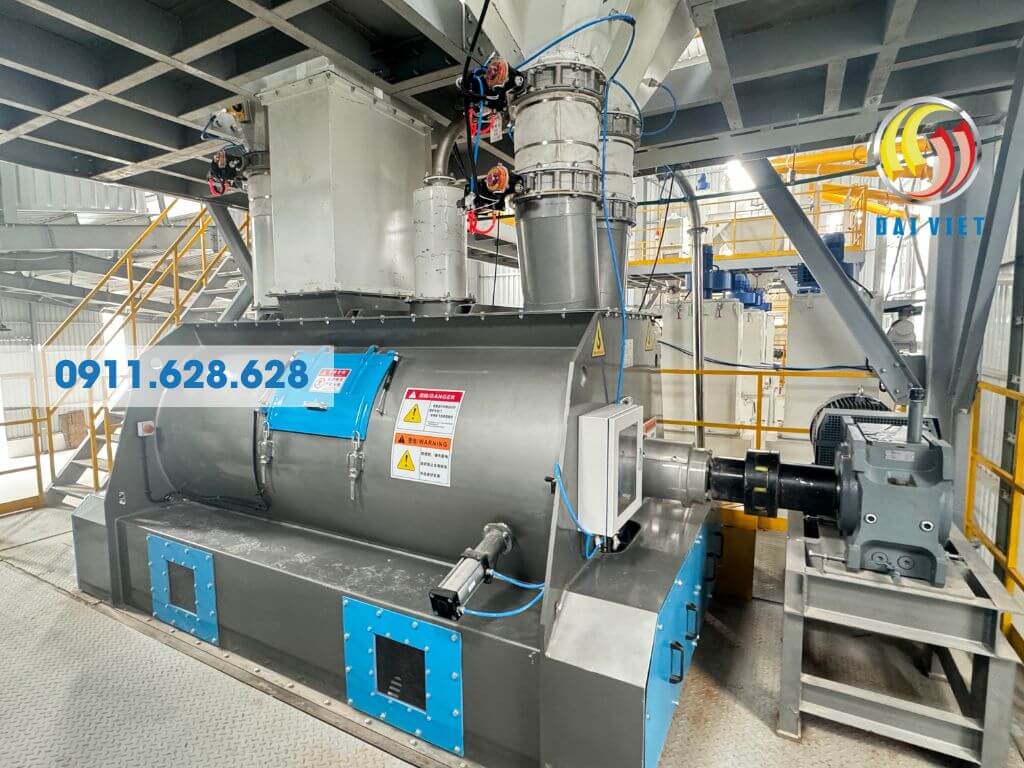
Hình ảnh hệ thống trộn sản xuất vữa khô và keo dán gạch trước khi đi vào vận hành dây chuyền vữa khô
- Phương thức hoạt động: Nguyên liệu từ hệ thống cân định lượng được nạp vào máy trộn qua phễu trên.
- Máy trộn một trục: Trục quay với tốc độ 100-150 vòng/phút, lưỡi trộn đẩy nguyên liệu theo một hướng, tạo dòng tuần hoàn đều đặn.
- Máy trộn hai trục: Hai trục quay ngược chiều (120-180 vòng/phút), lưỡi trộn tạo lực cắt và đối lưu mạnh, tăng hiệu quả trộn 20-30% so với máy một trục.
- Hỗn hợp hoàn thiện được xả qua van đáy (đường kính 200mm) trong 1-1,5 phút.
- Sự cố tiềm ẩn:
- Lưỡi trộn mòn hơn 15% sau 5000 giờ vận hành, làm giảm độ đồng đều 10-15%.
- Trục quay rung do vòng bi hỏng khi nhiệt độ vượt 90°C sau thời gian dài chạy liên tục.
- Lưu ý:
- Kiểm tra độ mòn lưỡi trộn bằng thước kẹp (sai số ±0,01mm), thay lưỡi sau 5000 giờ bằng thép chịu mòn chất lượng cao.
- Bổ sung mỡ chịu nhiệt (NLGI 2) cho trục quay mỗi 50 giờ; ưu tiên sử dụng máy hai trục cho sản lượng lớn.
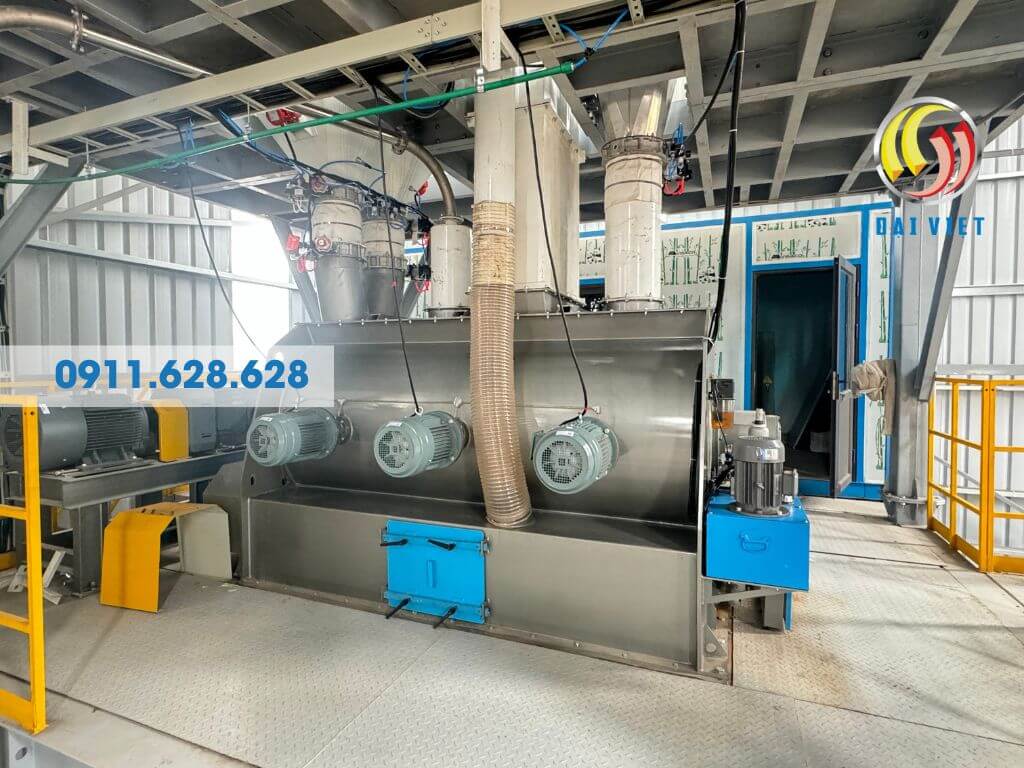
Hình ảnh hệ thống trộn sản xuất vữa khô và keo đang chuẩn bị hoàn thiện để chạy vận hành dây chuyền vữa khô
2.5. Hệ thống đóng bao
- Cấu tạo: Máy đóng bao tự động (công suất 400-600 bao/giờ), phễu định lượng (dung tích 0,5-1 tấn), máy may bao (tốc độ 10-15 giây/bao), băng tải (rộng 0,6m, dài 6-10m).
- Chức năng: Đóng gói vữa khô thành các bao 25kg hoặc 50kg với độ chính xác cao, thuận tiện cho vận chuyển và sử dụng.
- Phương thức hoạt động: Hỗn hợp từ máy trộn được nạp vào phễu, hệ thống cân định lượng đảm bảo sai số ±50g/bao, máy may bao khâu kín với mật độ 5-7 mũi/cm. Băng tải vận chuyển bao với tốc độ 0,5-1 m/s.
- Thông số kỹ thuật:
- Khối lượng bao: 25kg (±50g) hoặc 50kg (±100g).
- Công suất: 10-15 tấn/giờ (tương đương 400-600 bao).
- Sự cố tiềm ẩn:
- Phễu định lượng tắc do vữa khô vón cục khi độ ẩm vượt 0,5%.
- Kim may gãy sau khi khâu 2000-3000 bao.
- Lưu ý: Vệ sinh phễu bằng khí nén áp suất 6 bar sau mỗi ca; dự trữ kim may (thép không gỉ, dài 50mm) để thay thế kịp thời đảm bảo vận hành dây chuyền vữa khô an toàn, hiệu quả.
2.6. Hệ thống robot bốc xếp tự động
- Cấu tạo: Robot công nghiệp 4-6 trục (tải trọng 50-200kg), cánh tay dài 1,5-2m, hệ thống điều khiển PLC, băng tải đầu ra (dài 10-15m).
- Chức năng: Tự động xếp bao lên pallet với tốc độ 10-20 bao/phút, giảm sức lao động và tăng hiệu quả lưu kho.
- Phương thức hoạt động: Robot nhận tín hiệu từ PLC, gắp bao từ băng tải (tốc độ 0,5-1 m/s) và xếp thành chồng cao 1,5-2m (10-12 lớp/pallet). Tốc độ bốc xếp đạt 600-1200 bao/giờ.
- Thông số kỹ thuật:
- Tải trọng tối đa: 200kg (tương đương 4 bao 50kg).
- Độ chính xác vị trí xếp: ±2mm.
- Nguồn điện: 380V, 50Hz, công suất 5-10kW.
- Sự cố tiềm ẩn:
- Cánh tay robot lệch ±5mm do cảm biến vị trí hỏng.
- Động cơ quá tải khi nhiệt độ vượt 85°C sau 24 tiếng vận hành liên tục.
- Lưu ý: Hiệu chuẩn cảm biến vị trí mỗi 6 tháng; kiểm tra nhiệt độ động cơ bằng súng đo hồng ngoại để tránh quá nhiệt. Điều này rất quan trọng để đảm bảo vận hành dây chuyền vữa khô hiệu quả.
2.7. Hệ thống khử bụi
- Cấu tạo: Túi lọc xung (100-200 túi, diện tích lọc 50-100 m²), quạt hút (10-20kW, lưu lượng 10.000-20.000 m³/h), ống dẫn khí (đường kính 400-600mm).
- Chức năng: Thu gom bụi từ lò sấy và máy trộn, đảm bảo nồng độ bụi thải dưới 20mg/Nm³ theo QCVN 05:2013/BTNMT.
- Phương thức hoạt động: Bụi được hút qua ống dẫn, giữ lại trong túi lọc nhờ xung khí nén (6 bar, tần suất 10-15 giây/lần). Bụi rơi xuống phễu để tái sử dụng.
- Thông số kỹ thuật:
- Hiệu suất lọc: 95-99%.
- Áp suất hút: 1500-2000 Pa.
- Sự cố tiềm ẩn:
- Túi lọc thủng sau 6-8 tháng sử dụng liên tục.
- Quạt hút yếu do cánh mòn, giảm hiệu suất 40%.
- Lưu ý: Thay túi lọc (vải polyester) mỗi 6 tháng; đo áp suất hệ thống bằng manometer (sai số ±10 Pa) hàng tuần.
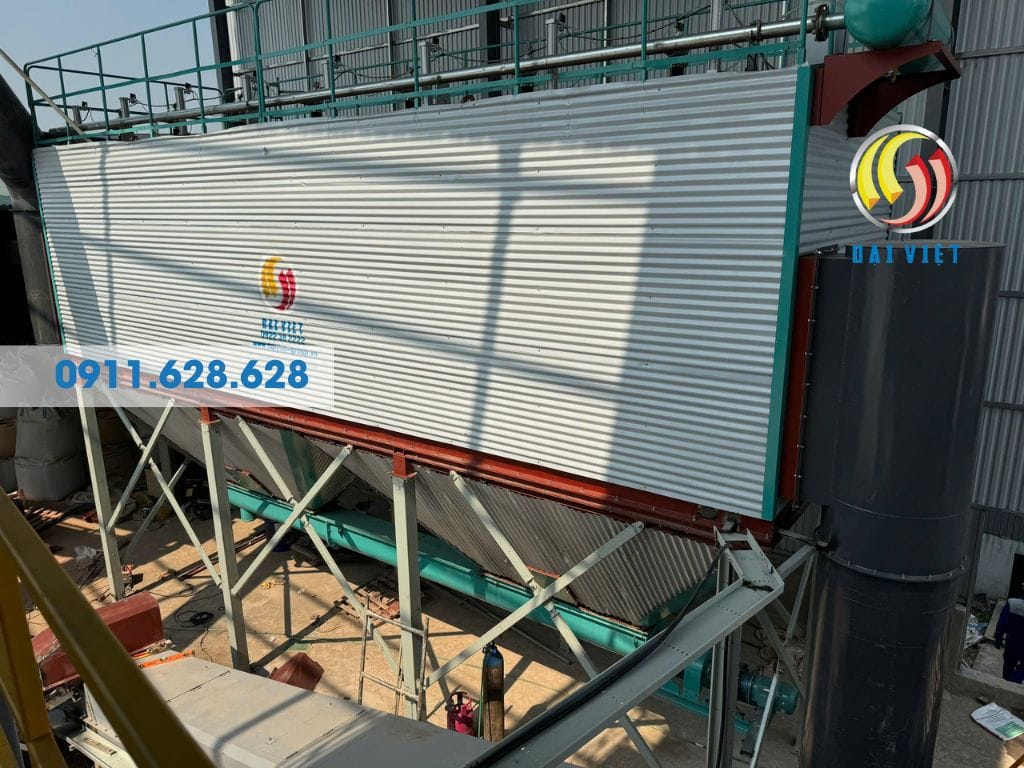
Hình ảnh lắp đặt hệ thống thu bụi cho dây chuyền vữa khô với buồng chứa các túi lọc – Kiểu thu bụi dạng xung trước khi vận hành dây chuyền vữa khô
3. Quy trình vận hành dây chuyền vữa khô
3.1. Vận hành ca tiêu chuẩn (8:00 – 16:00)
- 8:00 – 8:30: Kiểm tra áp suất silo, khởi động lò sấy (15 phút đạt nhiệt độ khí đầu vào 400°C, cát đầu ra 60-70°C), chạy thử vít tải và máy trộn.
- 8:30 – 15:30: Sản xuất liên tục với công suất 20-30 tấn/giờ, đạt tổng sản lượng 140-210 tấn/ca.
- 15:30 – 16:00: Dừng máy, vệ sinh phễu, vít tải và lưỡi trộn để tránh tích tụ nguyên liệu.
3.2. Tăng ca 24 tiếng
Trong trường hợp cần sản lượng cao, dây chuyền hoạt động 3 ca liên tục (8:00 – 16:00, 16:00 – 0:00, 0:00 – 8:00), đạt 480-720 tấn/ngày với công suất 20-30 tấn/giờ. Cần thực hiện bảo trì khẩn cấp mỗi 12 tiếng để đảm bảo thiết bị hoạt động ổn định.
Mô hình vận hành dây chuyền sản xuất vữa khô
4. Sự cố tiềm ẩn và biện pháp khắc phục trong vận hành dây chuyền sản xuất vữa khô
- Lò sấy: Nhiệt độ cát vượt 80°C – điều chỉnh đầu đốt, thay cảm biến nhiệt nếu sai số >0,5°C.
- Cân định lượng: Cảm biến lệch ±0,5kg – hiệu chuẩn bằng quả cân chuẩn 1 tấn.
- Máy trộn: Lưỡi trộn mòn – thay lưỡi mới (thép chịu mòn) sau 5000 giờ.
- Đóng bao: Phễu tắc – sử dụng khí nén 6 bar để làm sạch.
- Robot bốc xếp: Cánh tay lệch ±5mm – điều chỉnh hệ thống PLC để sai số dưới 2mm.
Tham quan vận hành dây chuyền vữa khô thực tế
5. Lưu ý quan trọng khi vận hành dây chuyền sản xuất vữa khô
- Nguyên liệu: Đảm bảo cát có kích thước hạt <5mm, độ ẩm <0,5% (đo bằng máy đo độ ẩm chuyên dụng); xi măng đạt tiêu chuẩn TCVN 2682:2009.
- Nhiệt độ: Lò sấy duy trì khí đầu vào 400-500°C, cát đầu ra 60-70°C (kiểm tra bằng nhiệt kế hồng ngoại); động cơ các bộ phận không vượt 85°C.
- Bảo trì: Vệ sinh lò sấy và vít tải hàng tuần; kiểm tra lưỡi trộn (máy một trục hoặc hai trục) mỗi tháng; thay túi lọc khử bụi sau 6 tháng.
- Dự trữ linh kiện: Chuẩn bị vòng bi (6205-2RS), kim may (dài 50mm), và túi lọc để thay thế khi cần.
Kết luận
Vận hành dây chuyền vữa khô đòi hỏi sự kiểm soát chặt chẽ các thông số kỹ thuật, từ nhiệt độ sấy cát (60-70°C đầu ra) đến hiệu quả trộn của máy một trục hoặc hai trục. Việc hiểu rõ chức năng của từng bộ phận, xử lý sự cố kịp thời và thực hiện bảo trì định kỳ là yếu tố quyết định để đạt hiệu suất tối ưu. Trong bối cảnh nhu cầu vật liệu xây dựng tăng trưởng ổn định, dây chuyền sản xuất vữa khô là giải pháp hiệu quả để đáp ứng yêu cầu của ngành.
Cập nhật ngày: 24/03/2025. Đây là một bài viết tổng quan, thông tin mang tính chất tham khảo. Hãy liên hệ 0911.628.628 để được tư vấn chuyên sâu và chính xác hơn!
Xem bài viết tương tự cùng chủ đề:
- Công nghệ đóng bao vữa khô trong sản xuất hiện đại
- Dây Chuyền Sản Xuất Vữa Khô A – Z– Tương Lai Của Ngành Vật Liệu Xây Dựng